Industry 4.0 is revolutionizing manufacturing, and mechatronics is at the heart of this transformation. From robotic automation to smart sensors and cyber-physical systems, this article explores how mechatronics integrates mechanical, electrical, and software engineering to drive innovation in modern industries.
Industry 4.0 represents the convergence of digital, physical, and biological systems, revolutionizing the manufacturing and automation sectors. At the core of this transformation is mechatronics, an interdisciplinary field combining mechanical engineering, electronics, computer science, and control engineering. Mechatronics is crucial in developing smart, automated, and interconnected industrial systems that characterize Industry 4.0.
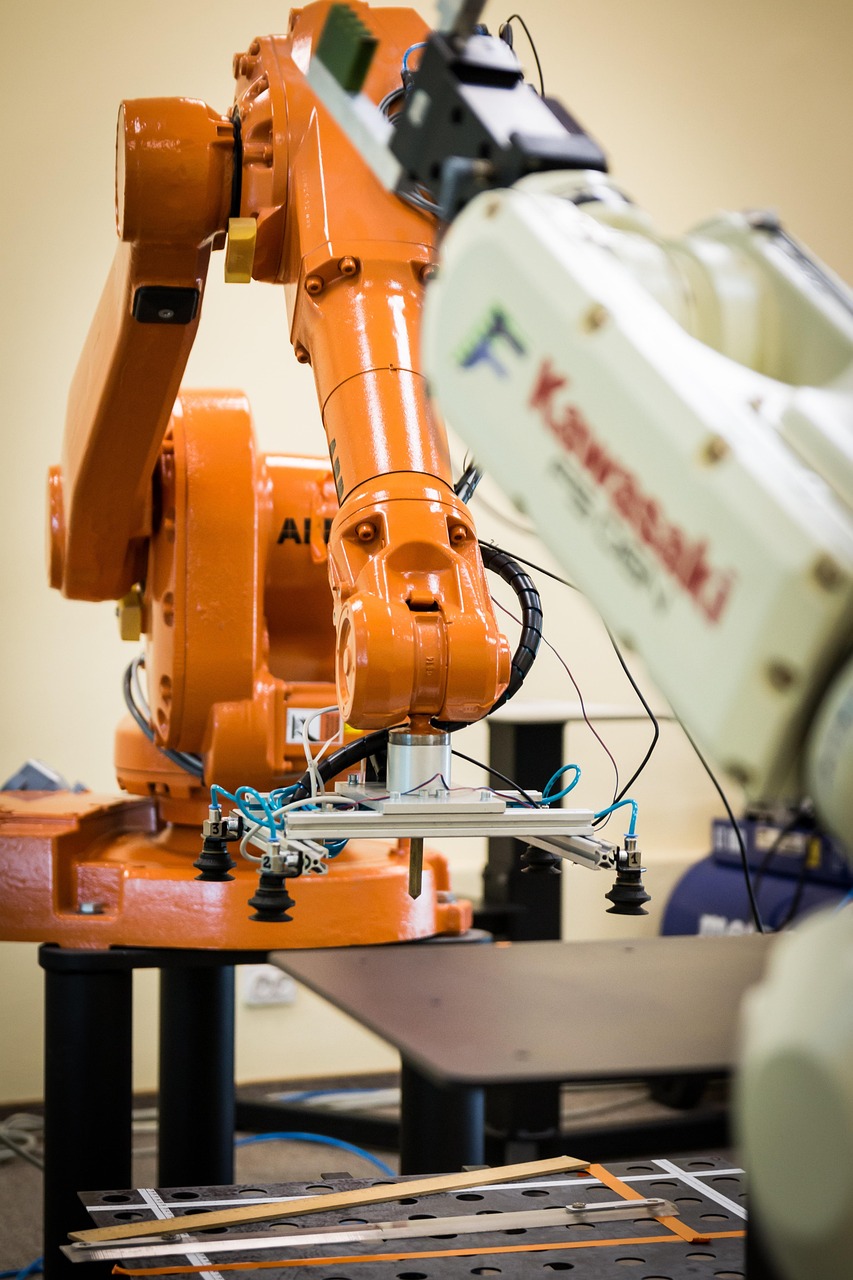
An automated production line integrating physical machinery with digital monitoring for enhanced efficiency. Image used courtesy of Pixabay.
The Pillars of Mechatronics in Industry 4.0
1. Cyber-Physical Systems (CPS) and Mechatronics
Cyber-Physical Systems (CPS) integrate computational and physical processes, enabling real-time monitoring, control, and data analysis. Mechatronic systems incorporate CPS principles to create intelligent machines that communicate, analyze, and optimize operations autonomously.
2. Industrial Internet of Things (IIoT)
Mechatronics plays a vital role in IIoT by embedding sensors, actuators, and connectivity into industrial equipment. This enables real-time data acquisition, predictive maintenance, and remote diagnostics, reducing downtime and improving efficiency.
3. Automation and Robotics
Industry 4.0 heavily relies on advanced robotics and automation, both of which are powered by mechatronics. From collaborative robots (cobots) to autonomous mobile robots (AMRs), mechatronic engineering ensures seamless integration between hardware, software, and control algorithms.
4. Artificial Intelligence and Machine Learning
Mechatronics systems leverage AI and machine learning to enhance decision-making processes. These technologies allow robots and automated systems to learn from data, adapt to dynamic conditions, and optimize industrial workflows.
5. Digital Twin Technology
Digital twins create virtual representations of physical assets, enabling simulations, real-time monitoring, and performance analysis. Mechatronic components, combined with advanced sensors and AI, make it possible to develop accurate and functional digital twins for predictive maintenance and process optimization.
Benefits of Mechatronics in Industry 4.0
- Increased Efficiency: Automated mechatronic systems enhance precision and productivity.
- Reduced Downtime: Predictive maintenance prevents unexpected failures.
- Enhanced Flexibility: Adaptive mechatronic systems respond dynamically to changing production needs.
- Cost Savings: Automation reduces labor and operational costs.
- Improved Safety: Intelligent machines minimize human exposure to hazardous environments.
Challenges and Future Outlook
Despite its advantages, integrating mechatronics into Industry 4.0 faces challenges such as high initial costs, cybersecurity risks, and the need for specialized skills. However, advancements in AI, cloud computing, and edge computing will continue to enhance mechatronic systems, making Industry 4.0 more efficient and resilient.
Industry 4.0
Mechatronics is the backbone of Industry 4.0, driving automation, intelligence, and interconnectivity in modern industries. As technology evolves, mechatronics will play an even more critical role in shaping the future of smart manufacturing and industrial automation.